Porosity in Welding: Identifying Common Issues and Implementing Ideal Practices for Avoidance
Porosity in welding is a pervasive issue that usually goes undetected up until it causes substantial issues with the integrity of welds. In this conversation, we will certainly check out the crucial aspects contributing to porosity formation, analyze its harmful effects on weld performance, and go over the best techniques that can be adopted to minimize porosity occurrence in welding procedures.
Usual Sources Of Porosity
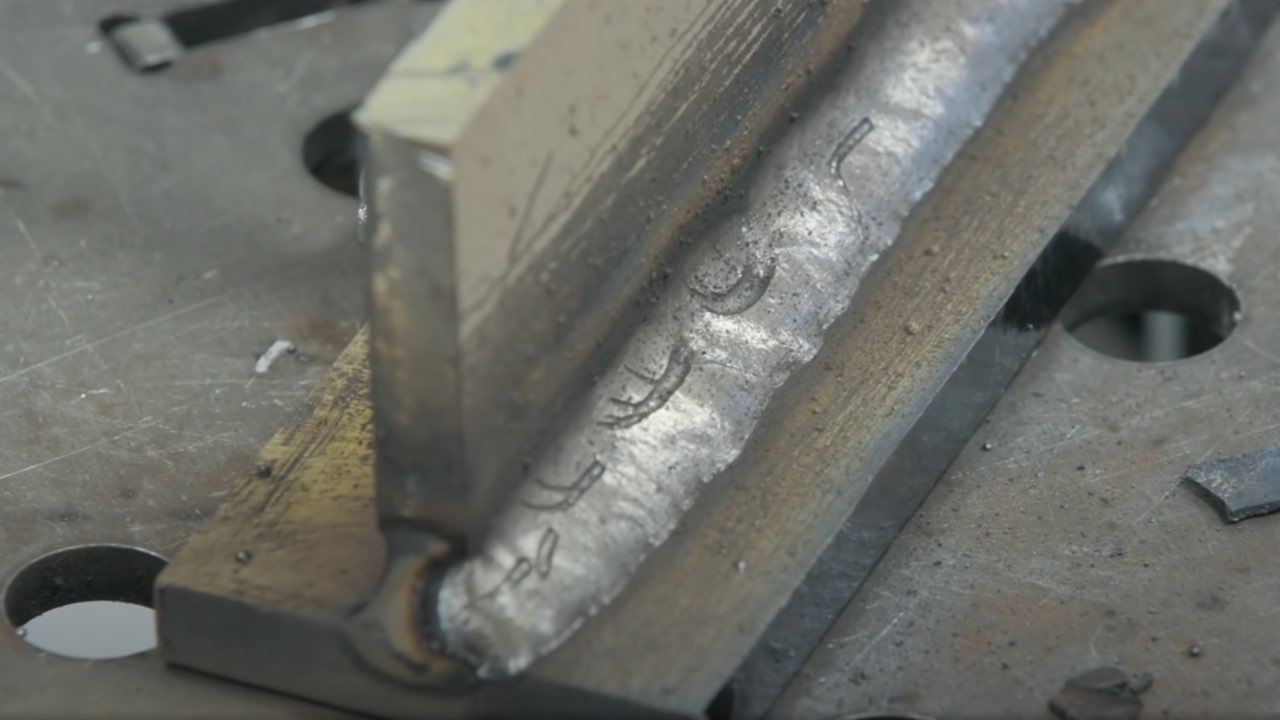
Utilizing unclean or wet filler products can present impurities into the weld, adding to porosity issues. To alleviate these usual causes of porosity, extensive cleansing of base metals, correct securing gas selection, and adherence to ideal welding criteria are important practices in achieving top quality, porosity-free welds.
Impact of Porosity on Weld Top Quality

The visibility of porosity in welding can substantially compromise the architectural honesty and mechanical buildings of bonded joints. Porosity creates voids within the weld metal, compromising its general toughness and load-bearing ability. These voids serve as tension focus points, making the weld more prone to splitting and failure under applied lots. In addition, porosity can reduce the weld's resistance to corrosion and other ecological aspects, even more diminishing its long life and performance.
Welds with high porosity degrees tend to display reduced effect stamina and decreased capacity to warp plastically prior to fracturing. Porosity can hamper the weld's capability to properly transmit forces, leading to early weld failure and prospective security threats in critical structures.
Best Practices for Porosity Avoidance
To resource enhance the structural stability and quality of welded joints, what certain actions can be executed to decrease the incident of porosity during the welding procedure? Making use of the correct welding technique for the specific product being bonded, such as readjusting the welding angle and weapon position, can additionally stop porosity. Routine evaluation of welds and instant removal of any type of issues determined throughout the welding process are important practices to prevent porosity and generate high-grade welds.
Value of Appropriate Welding Methods
Carrying out correct welding strategies is extremely important in making certain the architectural honesty and high quality of bonded joints, developing upon the foundation of reliable porosity avoidance steps. Too much warmth can lead to boosted porosity due to the entrapment of gases in the weld swimming pool. Furthermore, utilizing the suitable welding parameters, such as voltage, current, and take a trip rate, is critical for attaining audio welds with minimal porosity.
Additionally, the selection of welding procedure, whether it be MIG, TIG, or stick welding, should align with the specific demands of the task to ensure ideal results. Proper cleansing and prep work of the base metal, as well as picking the appropriate filler product, are also important elements of efficient welding strategies. By sticking to these best methods, welders can lessen the danger of porosity development and generate high-grade, structurally audio welds.
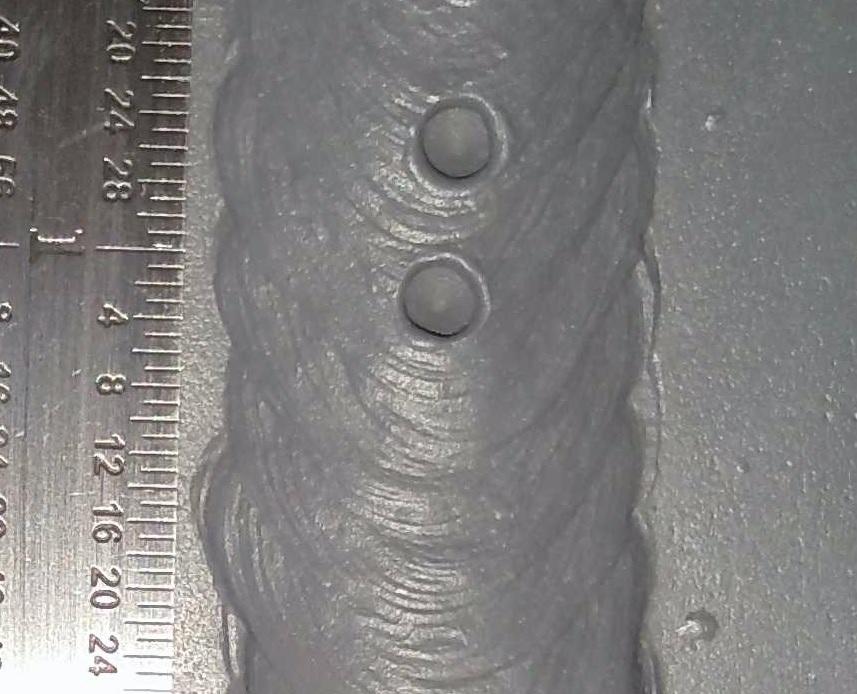
Checking and High Quality Control Procedures
Quality his explanation control steps play a critical duty in verifying the integrity and integrity of bonded joints. Evaluating procedures are necessary to find and prevent porosity in welding, ensuring the stamina and resilience of the final item. Non-destructive screening approaches such as ultrasonic testing, radiographic testing, and aesthetic inspection are frequently utilized to recognize prospective defects like porosity. These methods permit the analysis of weld top quality without endangering the honesty of the joint. What is Porosity.
Post-weld inspections, on the various other hand, analyze look these up the last weld for any problems, consisting of porosity, and confirm that it satisfies defined standards. Carrying out a comprehensive high quality control strategy that includes comprehensive screening treatments and evaluations is vital to reducing porosity issues and guaranteeing the general top quality of bonded joints.
Verdict
To conclude, porosity in welding can be a common problem that influences the top quality of welds. By identifying the typical sources of porosity and carrying out ideal techniques for avoidance, such as proper welding strategies and testing actions, welders can ensure top quality and dependable welds. It is vital to focus on avoidance approaches to lessen the occurrence of porosity and maintain the honesty of welded frameworks.